Fabrication and Press Brake
At AMR we are not just a Laser Cutting Company, we also offer an in-house fabrication and Press Brake service , to help our customers meet their project deadlines.
FOLDING
AMADA HFE – 80-25 Press Brake
The HFE generation of press brake, are ideally suited for producing complex components with tight tolerances
This is a 7 axis CNC , which delivers 80MT of bending force over 2570mm.
Programmed using 2D software and a wide range of Digitised tooling to draw the part profile, it calculates the developed length, backgauge axes position, punch penetration, spring back and detects collisions between part and machine.
It also has a patented digital protractor linked to the numerical control, this device ensure accurate measurements of the bent angle.
The operator ca simply use the function button which transmits the measured angle value to the control, which then recalculates the punch penetration giving a perfect angle.
This offers a more precise, repeatable, quality component than that produced by traditional press braking.

FABRICATION
Our fabrication & welding facility exceeds 3,000 sq.m [32,000 sq.ft] and is serviced with overhead cranes offering combined lifting up to 48te with 6.5m below the hook.
We have teams of highly skilled operatives and coded welders to ensure an efficient manufacturing service.
Guillotines: Cutting up to 3,000mm in length and 12.5mm plate thickness
Pressbrakes and plate benders: forming up to 3,500mm in length and 20mm plate thickness
Plate rollers: forming up to 2,500mm in length and 25mm plate thickness
Punching and shearing: up to 20mm plate thickness
Saw cutting: up to 330mm diameter tube and 460mm (W) x 305mm (H) rectangular @ 0°
Flame & plasma cutting: up to 100mm plate thickness
Drilling: maximum 19″ Column, 6′ Arm, Spindle No. 5 Morse Taper
Welding: MAG, FCAW UP TO 450A; MMA (AC/DC) up to 650A; TIG up to 450A & Submerged Arc up to 650A
Weld Procedure Specifications (WPS) in accordance with BS EN ISO 15614-1:2017
Welder Approvals in accordance with BS EN 287-1: 2011
Weld Testing: non-destructive MPI, UT & Radiograph in accordance with British Standards
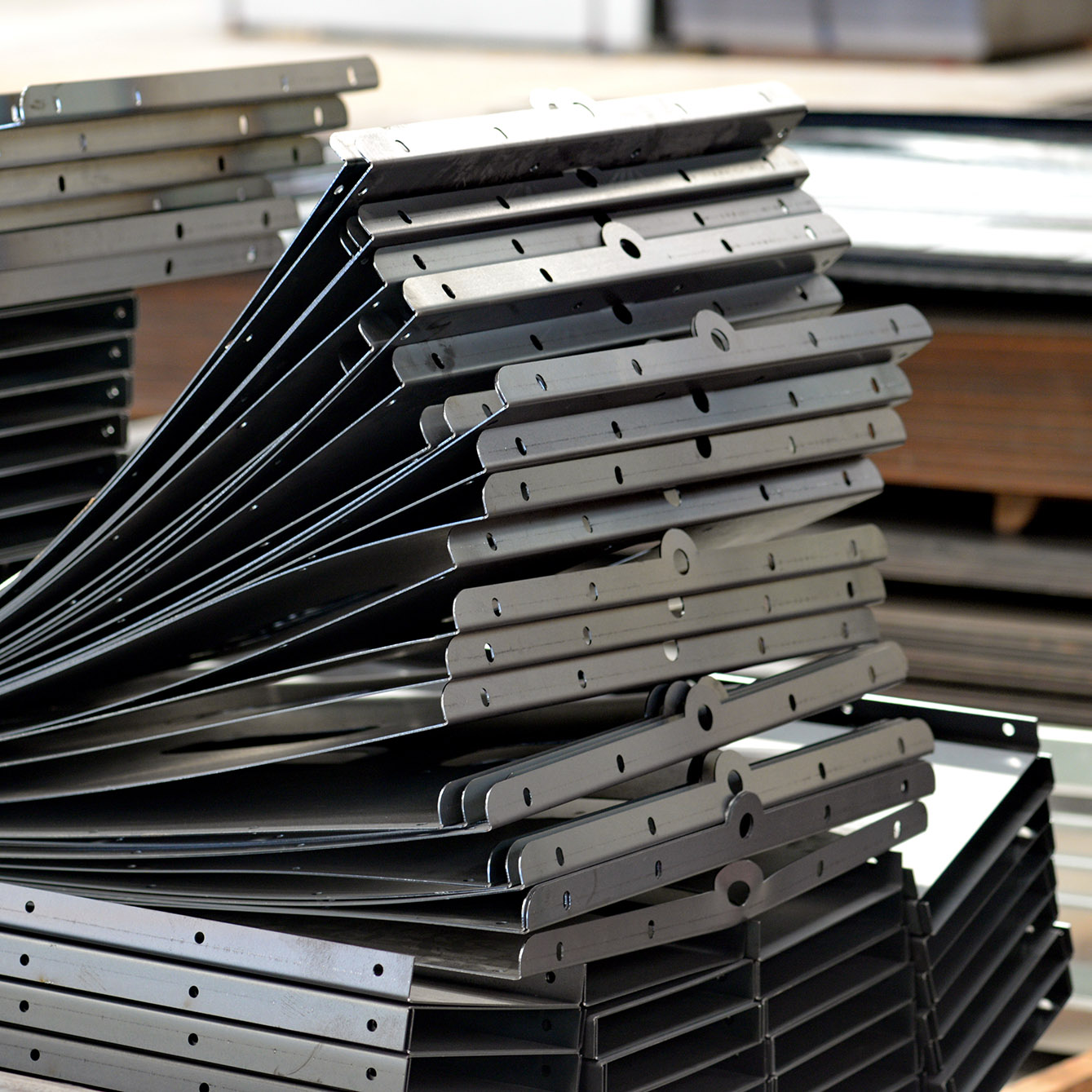
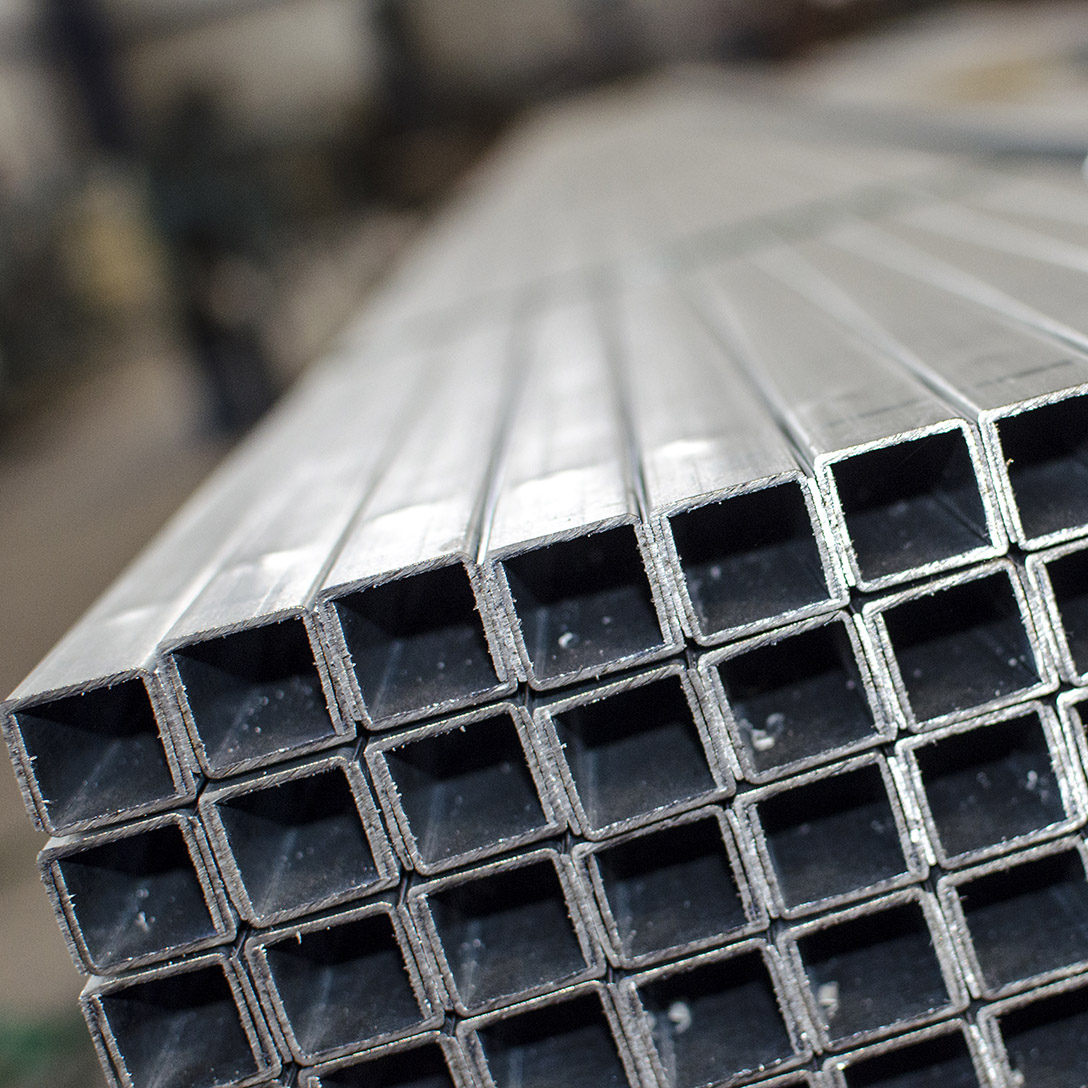
MACHINING
In excess of 650 sq.m (7,000 sq.ft.) and serviced with 5te overhead cranes, our machine shop capabilities include capacity for drilling, turning and milling with both CNC and conventional equipment.
From one-off components to batch projects, we offer a quality product and competitive prices.
Drilling
- Asquith-Archdale Model 6PT 19-72, S# P31068, 19″ Column, 6′ Arm, Spindle No. 5 Morse Taper, 18 Spindle speeds from 9.5 to 1,560 rpm, Power cross travel, 20hp 220/440v 3ph
Herbert twin pedestal drill with automatic tapping head
Boring
- Webster Bennet, 48″ Swing, 24″ Daylight
Webster Bennet, 60″ Swing, 24″ Daylight
Automatic Cutting Band Saw
- Amada HA-250W up to 250mm diameter tube and 300mm (W) x 250mm (H) rectangular @ 0°
Lathes
- 2 No. Colchester TORNADO bar fed CNC lathe: 85mm bar capacity; sliding head; 8 turret tool station
- Harrisons Alpha 400 Plus: 320mm swing, 1m between centres H
- Harrisons M450 2 Metre B/C Swing 350
- Harrisons M600 1½ Metre B/C Swing 300
- Harrisons M350 1½ Metre B/C Swing 300
Milling
- CNC Ajax bed mill capacity: X-1,400 mm Y-1000 mm & Z-1000 mm
- CNC Laguna bed mill capacity: X-1,800 Y-1,000 mm & Z-1,000 mm
- CNC Huron 5 axis machining centre: X-1,200 mm, Y-800 mm & Z-800 mm
- DRO Elgamill CS10 6m: X-4,300 mm Y-1,000 mm & Z-1,000 mm
BLASTING & PAINTING
An ICATS registered company with qualified applicators and ICorr certified Paint Inspectors to ensure the highest quality of workmanship.
Self-Contained Pressurised Blast Cabinet using Reclaimed Ali Oxide. Suitable for cleaning, removing light corrosion and other deposits, roughening, preparing surfaces and etching. Internal cabinet dimensions: 44″W x 26″D x 30″H
Grit Blasting
In our 300 sq.m (3,200 sq.ft)blast facility using SFEG AH-24 portable abrasive blast pots, our facility operates chilled iron grit and can achieve steel surface preparation grades from Sa1 up to Sa3 in accordance with BS EN ISO 8501-1: 2007.
The blast medium is reclaimed and filtered using a grit recovery system.
Thermal metal spraying
Using Metallisation MK73-FS equipment our trained operatives are able to apply corrosion protection coatings of zinc, aluminium and zinc/aluminium alloys onto steelwork at thicknesses to suit your specification. Thermal metal spray is commonly used as an alternative to galvanising.
Industrial Coatings using Airless & Conventional spray
Utilising our spray rooms totalling 550 sq.m and Graco Merkur X48-1 high pressure airless spray units we are able to provide industrial coating systems to Network Rail and Highways Specifications and are approved to the National Highways Sector Scheme 19A for the corrosion protection of ferrous materials by industrial coating.
FREE QUOTE
Looking for a price on your next project?
Fill out this form to get in touch.
TELEPHONE
01282 448008
sales@lasercutters.co.uk
ADDRESS
Unit 3, Gannow Business Park, Gannow Lane, Burnley, Lancashire BB12 6JJ
TELEPHONE
01282 448008
sales@lasercutters.co.uk
ADDRESS